
And what would our visualization guy say? What about the product manager who focused on model based definition for the past year? We’ll ask them and many other product managers for their picks in coming weeks. We suspect our manufacturing expert might choose three other features entirely. Of course, this is all just Martin’s opinion.
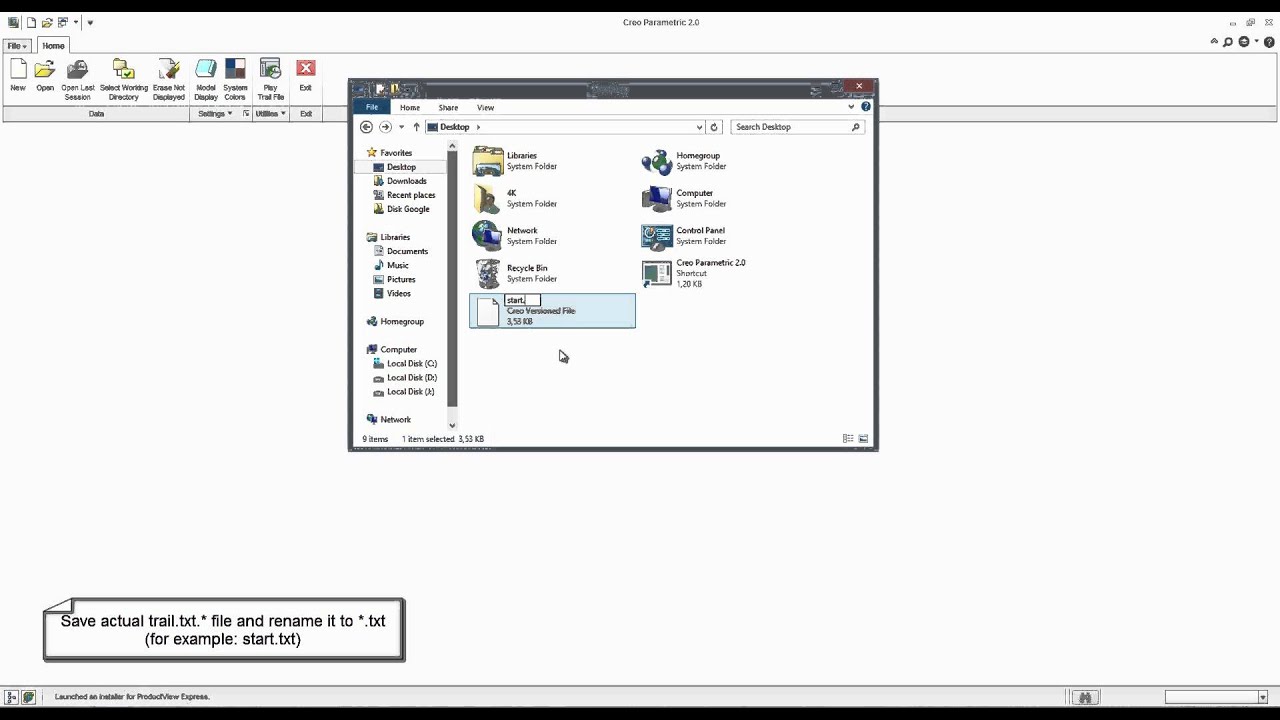
These enhancements give you more precision over the geometry and a more predictable regeneration of Extrude and Revolve features. You won’t need to create intermediate construction features, which were previously required. Extrude with offset: An option has been added to the Extrude tab to either offset or transform the surface reference, To Selected.This makes it simple to define geometry that has an offset. Negative direction: With the Extrude and Revolve tools, you can now specify negative direction values for one side, so that material operation is inverted.This means you don’t have to navigate to the option panel on the dashboard each time. Side 2 access: You have access to side 2 options directly from the graphics window when you right-click on a feature.The Creo 4.0 release includes major enhancements related to extrude/revolve functionality: Neumueller demonstrates in the video below: More Control Over Geometry When Manipulating Sketch-Based Featuresįor those working with sketch-based features, you’ll notice that it’s faster and easier to manipulate geometry. This functionality makes it so late-stage design changes are quicker and easier to complete, editing imported data is effortless, and simplifying designs for downstream analysis takes just minutes. New flexible modeling sheet metal enhancements make it simple to edit this bend and relief. Working with sheet metal has never been easier. And quickly change design intent characteristics individually or globally. Edit sheet metal bends, bend reliefs, corner reliefs, corner seams, and forms. One of Creo’s most powerful capabilities, flexible modeling, now extends to sheet metal. Plus, you can easily propagate customizations to other nodes (stay tuned to this blog to find out how). Even better, we’ve streamlined the process for setting up these customizations. Keyboard shortcuts can also be configured. You can customize options on ribbons, shortcut menus, and mini toolbars. You can now add those seconds back into your day by customizing Creo to show the option where you want to see it. Each time you add one, you spend a few seconds locating the Form > Die Form option on the Model tab. Let’s say your workflow has you adding die forms to your models regularly. New customization options make it easier and more streamlined for you to tailor the tool for optimal productivity. The new mini-toolbar gives you access to relevant options while also keeping your focus on the graphics area. It puts context-sensitive commands right at your fingertips-no need to go to the model tree or ribbon to find a command. What does that mean? Throughout Creo Parametric you’ll find a new intelligent mini-toolbar.
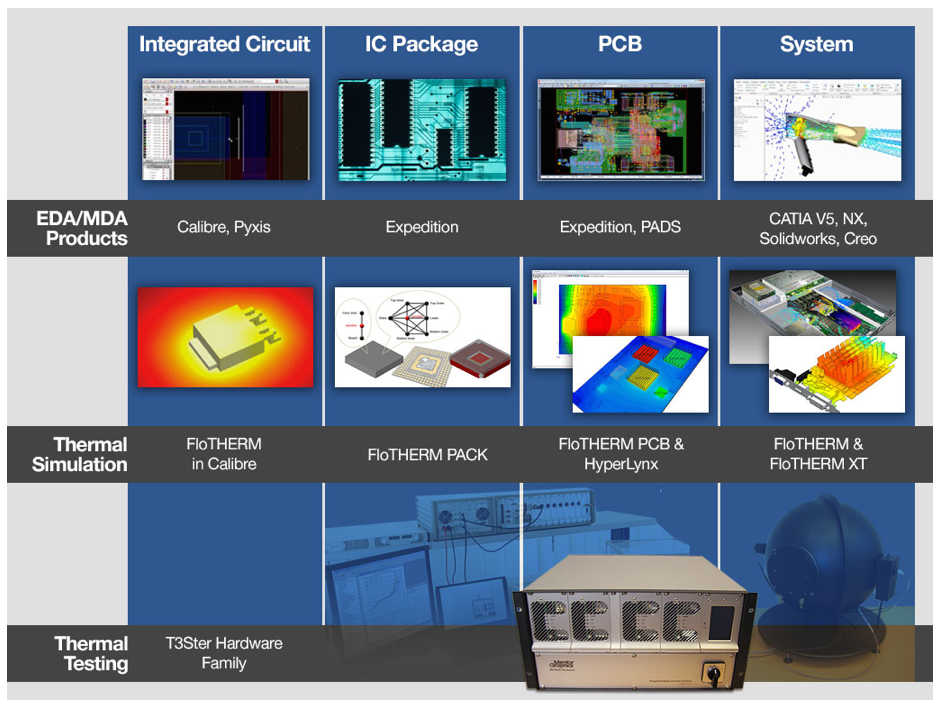
To make it so your eyes never leave your design, we introduced a new interaction paradigm. Martin Neumueller recently delivered a presentation highlighting several new Creo Parametric capabilities and enhancements that are included in the Creo 4.0. He named four (I told you it was difficult):
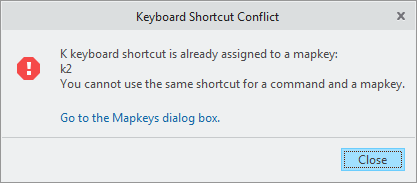
So, I asked Martin Neumueller, Product Management Senior Director, to name just the top three enhancements. For the first time, CAD users could directly open SolidWorks, CATIA, and NX files in their Creo software.īut the answer isn’t as straightforward with this newest release. In Creo 3.0, Unite technology clearly stood out from the pack. “Just out of curiosity, what is THE new enhancement in Creo 4.0? What do you think?” All of these improvements mean you can be even more productive while designing excellent products.īut with the release came an interesting question from our social media community.
#Ptc creo 5.0 controls and shortcuts update#
This latest update to our flagship 3D CAD software includes hundreds of core enhancements, not to mention breakthrough capabilities in additive manufacturing, model based definition (MBD), and smart connected design.
